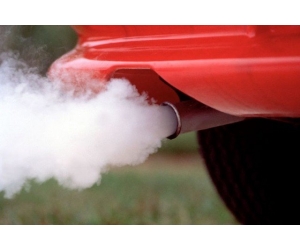
Выделим основные эксплуатационные факторы, которые
способствуют коррозии: это сплошная внешняя коррозия; коррозия, образовавшаяся
под действием деформации и нагрузок; сплошная внутренняя коррозия; коррозия,
образовавшаяся из-за высокой температуры; местная коррозия, образовавшаяся в
местах сварки, в зазорах и щелях.
Причиной сплошной внутренней коррозии становятся образования,
которые появляются при сгорании топлива, азота, воды, окислов углерода и серы.
Стоит отметить, что некоторые из них считаются сильными окислителями металла. Помимо
этого, в этилированном топливе содержатся рафинирующие добавки в виде бромидов
и хлоридов. Эти добавки образуют соляную и бромисто-водородную кислоты.
Коррозия глушителя изнутри ускоряется за счет влияния
нагара, который образуется во время работы мотора. При резкой смене температур
слой нагара подвергается большим напряжениям, так как коэффициент теплового
расширения материала глушителя и слоя нагара сильно отличается, отчего он
начинает отслаиваться, открывая при этом ту поверхность металла, которая не
защищена, поэтому она быстро и легко ржавеет.
Причины разрушения наружной поверхности выпускной системы —
увеличение температуры металла от соприкосновения с отработавшими газами.
Другая причина разрушения — это попадание на поверхности системы соли, водяных
брызг, грязи.
Чтобы хоть как-то систему выпуска и двигатель защитить от
коррозии применяют разные способы. Например, в США и в некоторых других странах
90% глушителей производят из алюминированной стали. На поверхность такой стали
диффузионным методом наносится смесь порошков оксидов алюминия и алюминия.
Долговечность глушителя при этом возрастает раза в два-три. В Великобритании
для изготовления глушителей берут сталь, в которой содержатся 36% титана и 11% хрома. Еще для изготовления
глушителей идет сталь, легированная молибденом.
Наиболее эффективно защищает наружные поверхности системы
выпуска от коррозии их окраска. Однако окрашивая поверхности системы нужно
брать во внимание, что температура отработавших газов у выпускного трубопровода
колеблется от 420°С до 760°С. Тогда как температура
металла выхлопной трубы колеблется от 200°С до 540°С. Следовательно, окрашивать
систему выпуска следует исключительно термостойкими, в основном
кремнийорганическими лаками и эмалями. Термостойкость лака можно увеличить
добавлением 6-10% алюминиевой пудры. Пудра добавляется в лак исключительно
перед его применением, потому что пудра при длительном хранении (больше 4
часов) начинает терять свою способность всплывать, из-за чего ухудшается
внешний вид покрытий и эксплуатационные показатели. Термостойкость
кремнийорганических лаков и эмалей после добавления алюминиевой пудры такова: КО-811,
а также КО-814 — до четырехсот градусов;
КО-88, а также КО-815 – до пятисот градусов;
КО-83 – до 420 градусов.
Эмаль КО-828 имеет алюминиевый цвет и используется для
окраски поверхностей системы выброса. Поверхности, обработанные этой эмалью,
имеют хорошую адгезию, влагостойкость и солестойкость и могут выдержать температуру
до 400°C. На поверхности системы эмаль наносится методом пневматического
распыления, а в качестве растворителя используется РКБ-1 или сольвент. Покрытие
сушится в течение получаса при 130°C.
Подобная эмаль наносится на металл двумя слоями, при этом
грунт наносить не нужно. Наносится слой эмали, потом 5 минут выдержки на
воздухе и наносится второй слой эмали.
Если алюминиевая пудра была добавлена в лак КО-83, то его
нужно использовать в течение 6 часов. Если лак наносится при помощи
краскораспылителя, то он разводится растворителем №646 до такой вязкости 13-14
с по B3–4. Окрашенное покрытие сушится в течение двух часов при температуре
170-180°.
Эмали КО-811 бывают зеленого цвета, черного и красного
цвета, при температуре 200 градусов высыхают в течение двух часов. При
распылении вязкость должна быть 12–15 с по В 3–4.
Поверхности, покрытие полиамидным лаком, имеют достаточно
высокую термостойкость, адгезию к металлам. Такие поверхности также обладают
хорошей стойкостью к абразивному износу. Термостойкость покрытий значительно
увеличивается за счет добавления 20% алюминиевой пудры.
Также существуют и другие методы защиты системы выпуска от
коррозии, которыми пользуются и автолюбители и мастера. Например, такой —
поверхность глушителя и выпускной трубы очищается от рыхлой ржавчины и грязи,
затем покрывается графитовой смазкой (наносить нужно тонким слоем). После того, как смазка обгорит, она оставит
после себя прочную противокоррозионную пленку черного цвета, которая и защитит
детали от коррозии.