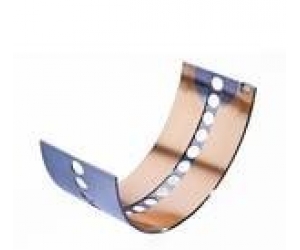
Современные двигатели внутреннего сгорания работают в условиях высоких нагрузок различного происхождения, перепадов температуры и давления, и потому эти нагрузки на движущиеся части двигателя - коленвал и распределвал, шатуны, толкатели и другие детали нуждаются сегодня в принципиально новых материалах, подобранных с учетом условий их работы. В двигателе постоянно что-то трется и вращается, и потребность в подшипниках всех типов чрезвычайно высока. Сейчас основным путем их совершенствования считается улучшение свойств и качества материалов, из которых они изготавливаются. Старые проверенные и новые материалы, а также их комбинации ныне дают возможность конструкторам выбрать оптимальную конструкцию подшипника.
Подшипник скольжения представляет собой опору или направляющую машин или механизмов, где трение осуществляется в процессе скольжения друг по другу сопряжённых поверхностей. Подшипники скольжения делятся на радиальные и осевые (упорные) – по направлению восприятия нагрузки.
По конструктивным особенностям подшипники скольжения подразделяются на:
·самоустанавливающиеся,
·сегментные,
·самосмазывающиеся и т. д.
Еще одна классификация подшипников скольжения - по режиму смазки (делятся на гидродинамические и гидростатические, газодинамические и газостатические (в них роль смазки выполняют воздух или нейтральный газ), а также с твёрдой смазкой).
Вкладыш скольжения для двигателя используется в радиальных подшипниках скольжения и выполняется, как правило, в виде втулки с двумя вкладышами (редко их бывает и больше), которые частично либо полностью охватывают вал. Работают такие подшипники в основном в режиме жидкостного либо полужидкостного трения, при этом на поверхности вкладышей должен быть тонкий слой масла, который не допускает непосредственного контакта металла с металлом. Казалось бы, ничего сложного, но ведь на вкладыш скольжения действуют большие нагрузки и высокие температуры.
Именно из-за этих температур и нагрузок в материале, из которого сделан вкладыш, образуются раковины и трещины, а находящиеся в загрязненном масле твердые частицы царапают его поверхность, приводя к ускоренному его износу. Если давление масла недостаточно, то это грозит преждевременным разрушением вкладыша, полное же отсутствие смазки убивает сухой вкладыш всего за несколько часов. Губительной для вкладыша является и кислая реакция среды в картере.
Если износ вкладыша идет постепенно, то увеличение зазора гарантировано приводит к падению давления масла, и, как следствие – к ускорению самого процесса износа. Об этом свидетельствует, в первую очередь, повышенный шум шатунных вкладышей. В этом случае необходимо, не дожидаясь худшего, просто сменить вкладыши. Особенно это касается двигателей повышенной мощности, в первую очередь – для спортивных автомобилей и машин с форсированными моторами. Для них подбор вкладышей должен быть особенно тщательным – ведь у них нагрузки на все детали двигателя, включая и вкладыши, гораздо выше, чем у обычных авто.
Алюминиевые вкладыши.
Поэтому и материал, из которого изготавливается вкладыш для двигателя, подбирается особенно тщательно. И тут ведущие автопроизводители предлагают несколько вариантов решения данной проблемы. Алюминиевые вкладыши, как правило, устанавливаются в современные моторы, производимые на американском и азиатском континентах.
Автопроизводители старого света нередко пользуют медные и свинцовые сплавы, в основном на дизелях (они куда лучше переносят нагрузки). Основной метод изготовления вкладышей для двигателей – дешевое и высокотехнологичное литье.
И все-таки явными лидерами остаются вкладыши алюминиевые. На это есть несколько весомых причин. Не последнюю роль здесь играет экология - стремление снизить до минимума использование в автомобилестроении токсичного свинца и свинцовых сплавов. А широкое применение в авиастроении различных сплавов на основе алюминия позволило автомобилестроителям использовать прочные, легкие и проверенные в жесточайших условиях авиации материалы. И еще один важный момент – их сравнительная дешевизна как благодаря массовому производству, так и снижению заказов на алюминий для авиастроения после окончания «холодной войны».
В производстве вкладышей скольжения для двигателя используется несколько марок алюминиевых сплавов. Один из них – разработанный в 1994 году A-500, в составе которого присутствует 8% олова, 3% кремния и 2% свинца. Его наследник в автопроме - A-590 – принадлежит к поколению материалов, вообще не содержащих свинца. К тому же он куда прочнее и более износостойкий благодаря повышенному, по сравнению со своим предшественником, содержанию кремния (6% вместо 3%) и сниженному – олова (всего 4%). Это позволило использовать A-590 как в работающих с большой нагрузкой дизелях, так и в высокооборотных бензиновых двигателях.
Еще одно достоинство алюминиевых сплавов – их достаточная износостойкость, поскольку они и сами почти не истираются, и, соответственно, масло своими частицами не засоряют. Да и высокая температура плавления алюминия позволяет использовать вкладыши из него практически в любых типах двигателей, при регулярной замене масла.
Но высокая твердость алюминиевых сплавов имеет и свою обратную сторону - низкую возможность поглощения твердых частиц. Они, приносимые потоком масла, оставляют глубокие царапины на поверхности вкладыша.
В более мягких медно-свинцовых вкладышах эти частицы просто вязнут в поверхности вкладыша, не оставляя на ней бороздок. Поэтому они гораздо менее требовательны к чистоте масла и мелким дефектам на поверхности шеек вала.
Чтобы бороться с износом вкладышей, производители стали высверливать (шлифовать) их внутреннюю поверхность. Тогда на ней остаются микроскопические канавки, на которых прочно удерживается масляная пленка.