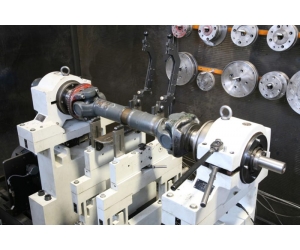
Статистика, как всегда, бесстрастна. Оказывается, 75% выброшенных деталей автомобиля не выработали свой ресурс. То есть, их можно было восстановить и использовать повторно. Например, большинство выбракованных по износу карданных валов теряют не более 2% от исходной массы. Прочность кардана при этом сохраняется. Конечно, восстановить изношенную деталь молотком и напильником не получится. Требуется специальное оборудование. Но его можно найти в любой более-менее серьёзной мастерской, и не обязательно автомобильной. Рассмотрим некоторые способы восстановления карданных валов.
Карданный вал исполняется в виде трубы, по обеим сторонам которой располагаются шарниры. Труба кардана очень прочная, ведь по ней передаются значительные усилия от коробки передач. Поэтому деформация, искривление карданных валов происходит не часто. Гораздо чаще валы подвергаются выработке, как правило, из-за воздействия грязи, влаги, агрессивных сред, абразивных веществ. То есть, в основном повреждается поверхностный слой. А эту беду уже давно научились «лечить» различными способами.
Порядок восстановления карданных валов
- Напыление, наплавка, сварка металлов. Химическая и гальваническая обработка.
- Далее потребуется использовать механическую обработку, чтобы удалить лишний нанесённый на поверхность вала металл, восстановить исходные геометрические размеры.
- После механической обработки мы получим требуемые размеры, но нанесённый слой металла ещё не соответствует повышенным механическим свойствам. Поэтому потребуется термическая обработка для получения необходимой твёрдости и прочих физико-механических свойств карданного вала.
- После термообработки происходит финишная механическая обработка – шлифование восстановленных участков, удаление фасок и т.д.
- Вместо термообработки и шлифовки можно воспользоваться более прогрессивным методом – накатыванием. Когда по реставрируемой поверхности специальным оборудованием «катают» ролик или шарик. В результате поверхностный слой уплотняется, соответственно повышается твёрдость напылённого металла и одновременно повышается чистота поверхности.
Наплавка металла
Восстановление валов наплавкой позволяет восстановить изношенные участки карданного вала, дополнительно повысить их износостойкость и долговечность путём нанесения металла необходимого химического состава с требуемыми физико-механическими свойствами.
Процесс наплавки технически несложен и производителен. Сначала присадочный металл расплавляется газопламенным, электродуговым или плазменным аппаратом, а затем переносится на восстанавливаемую поверхность карданного вала. Металл поверхностного слоя вала также расплавляется и «намертво» соединяется с расплавленным присадочным металлом. В результате образуется очень прочный слой наплавленного металла.
Напыление металла
При напылении расплавленный металл переносится потоком сжатого воздуха на заранее подготовленную поверхность карданного вала. Мощный поток воздуха распыляет расплавленный металл на мельчайшие частицы и разгоняет их. Частицы напыляемого металла с силой ударяются о поверхность вала и прочно с ней соединяются. Образуется восстановленный слой покрытия. Соединение происходит механически, и расплавлять металл самого карданного вала не требуется – это принципиальное отличие от наплавки.
Расплавлять присадочный металл удобнее высокотемпературным плазменным аппаратом. Источником плазмы служат азот или аргон. Аргон предпочтительнее, так как он защищает металл от окисления. В качестве напыляемых материалов используют специальные наплавочные порошки, порошковые проволоки или наплавочные проволоки сплошного сечения.
Гальваническое и химическое наращивание
Достаточно безопасный способ, но более длительный по времени. Гальваническое покрытие получается в результате переноса металла из электролита на поверхность карданного вала. Электролит – это водный раствор солей металла. Через электролит пропускается постоянный ток, в результате частички металлов «перетягиваются» на поверхность вала. Вал выступает в роли катода, а анодом является специальная металлическая пластина. В результате восстановленный слой получается очень аккуратным и требует меньше механической обработки.
Из химических методов чаще применяются фосфатирование и оксидирование.